ATTACK PLQ Bruksanvisning
Läs gratis den bruksanvisning för ATTACK PLQ (28 sidor) i kategorin Panna. Guiden har ansetts hjälpsam av 14 personer och har ett genomsnittsbetyg på 4.0 stjärnor baserat på 7.5 recensioner. Har du en fråga om ATTACK PLQ eller vill du ställa frågor till andra användare av produkten? Ställ en fråga
Sida 1/28
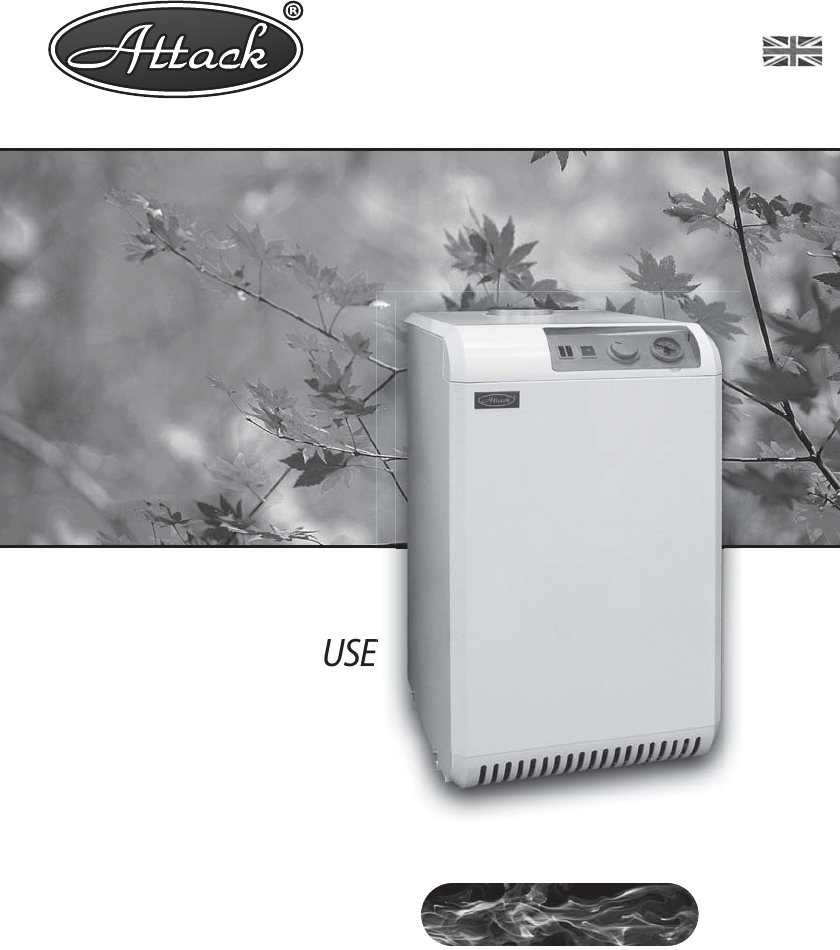
ATTACK®
CAST IRON FLOOR STANDING GAS BOILER
EKO, PLQ, KLQ, KLV, E, EZ, P
INSTRUCTION FOR USE
WWW.ATTACK.SK

2 |
Putting the boiler into operation:
ATTACK EKO, PLQ, KLQ, KLV, E, EZ, P
Capacity of 9, 12, 15, 20, 25, 30, 35, 40, 45, 49,9 kW
1. Plug the connector of the power supply flex into the 230 V/50 Hz socket. Test the socket with
another appliance. The main switch of the boiler must be in the „off“ position.
2. Let the gas flow into the boiler by turning a manual valve. When starting operation after a
longer period of inactivity, it is necessary to deaerate the gas piping. Force the air out by gas
through the burner (EKO, PLQ, P).
3. Set the thermostat to the maximum operation temperature.
4. Light the burner following the instructions on the internal side of the door (see more details in
the instructions EKO, PLQ, P).
5. Turn the boiler’s main switch on. The control light goes on and the main burner is ignited. Set
the thermostat back to the required temperature of the heating water.
6. To put the boiler out of operation for a short time, turn the main switch off and thereby, the
boiler remains in the stand-by mode, disconnected from power supply.
7. To put the boiler out of operation for a long time, turn the combined valve into the „off“ posi-
tion (see instruction EKO, PLQ, P), close the manual gas valve and put the power supply flex out
of the socket 230 V/50 Hz.
8. If it comes to the power failure during the operation, the gas supply into the burner is inter-
rupted, while the burner still burns (EKO, PLQ, P). When the power is supplied again, the burners
burn automatically without need of intervention.
9. For PLQ and KLQ modifications, the excessive output can be reduced by switching a button on
the front board. The excessive output is reduced automatically by the E and EZ modifications.
10. All the repairs during the guarantee and post-guarantee period have to be done by an author-
ized service organization.
ATTACK, s.r.o.
Vrútky

| 3
CAST IRON FLOOR STANDING GAS BOILER
Contents
Putting the boiler into operation ....................................................................................................................................................... 2
Introduction ................................................................................................................................................................................................ 4
General description ................................................................................................................................................................................. 4
Purpose of use ............................................................................................................................................................................................ 4
Modifications of the cast iron gas boilers ....................................................................................................................................... 5
Conditions of installation ...................................................................................................................................................................... 5
Conditions of operation ......................................................................................................................................................................... 6
Safety conditions ...................................................................................................................................................................................... 7
Examples of classification of the building materials by the inflammable level ................................................................ 7
Conditions to keep the ecological parameters ............................................................................................................................. 7
Technical description EKO, PLQ, KLV, KLQ, E, EZ, P types ........................................................................................................... 7
Electrical front panel of the EKO, PLQ, KLV, KLQ, E boilers ........................................................................................................ 8
Electrical front panel of the EZ boilers ............................................................................................................................................. 8
External dimensions of the EKO, KLV, PLQ, KLQ, P boilers ......................................................................................................... 9
Main parts of EKO, KLV, PLQ, KLQ, P boilers .................................................................................................................................... 9
External dimensions of E, EZ boilers .............................................................................................................................................. 10
Main parts of E, EZ boilers .................................................................................................................................................................. 10
Connecting the boiler to the electricity mains (not for ATTACK P boilers) ....................................................................... 11
Electrical equipment of boilers ......................................................................................................................................................... 11
Start – putting the boiler into operation ....................................................................................................................................... 11
Stop – putting the boiler out of operation .................................................................................................................................. 12
Operation control .................................................................................................................................................................................. 12
Failure states of operation .................................................................................................................................................................. 13
What to do in the case of failure ...................................................................................................................................................... 13
Chimney draught breaker .................................................................................................................................................................. 14
Function of the draught breaker ..................................................................................................................................................... 14
Function of the flue gas thermostat ............................................................................................................................................... 14
Boiler function ........................................................................................................................................................................................ 14
Output regulation ................................................................................................................................................................................. 14
After set up ............................................................................................................................................................................................... 15
Regulation of operation ...................................................................................................................................................................... 15
Marking of the boiler ............................................................................................................................................................................ 15
Spare parts ............................................................................................................................................................................................... 15
Guarantee, claim .................................................................................................................................................................................... 16
Service ........................................................................................................................................................................................................ 16
Maintenance ............................................................................................................................................................................................ 16
Packaging, transport, storing ............................................................................................................................................................ 16
Boiler accessories and documentation ......................................................................................................................................... 16
Technical changes ................................................................................................................................................................................. 16
Conclusion ................................................................................................................................................................................................ 17
Setting of the modulation electronics of the ATTACK EZ boiler ......................................................................................... 17
Technical data ......................................................................................................................................................................................... 18
Connecting the electrical installation of the ATTACK EKO boiler ....................................................................................... 19
Connecting the electrical installation of the ATTACK KLV boiler ........................................................................................ 19
Connecting the electrical installation of the ATTACK PLQ boiler ........................................................................................ 20
Connecting the electrical installation of the ATTACK KLQ boiler ....................................................................................... 20
Connecting the electrical installation of the ATTACK EZ boiler ........................................................................................... 21
Connecting the electrical installation of the ATTACK E boiler ............................................................................................. 21
Produktspecifikationer
Varumärke: | ATTACK |
Kategori: | Panna |
Modell: | PLQ |
Behöver du hjälp?
Om du behöver hjälp med ATTACK PLQ ställ en fråga nedan och andra användare kommer att svara dig
Panna ATTACK Manualer
4 April 2025
4 April 2025
31 Januari 2025
19 December 2024
19 December 2024
19 December 2024
19 December 2024
17 December 2024
Panna Manualer
- MTS
- Nefit
- Eldom
- De Dietrich
- Daalderop
- Siemens
- Elco
- Oertli
- ATAG
- AEG
- Inventum
- Worcester-Bosch
- TTulpe
- Viessmann
- Atlantic
Nyaste Panna Manualer
9 April 2025
8 April 2025
7 April 2025
7 April 2025
7 April 2025
7 April 2025
6 April 2025
6 April 2025