Gys Exagon 400 Flex CC/CV Bruksanvisning
Gys
Inte kategoriserad
Exagon 400 Flex CC/CV
Läs gratis den bruksanvisning för Gys Exagon 400 Flex CC/CV (104 sidor) i kategorin Inte kategoriserad. Guiden har ansetts hjälpsam av 14 personer och har ett genomsnittsbetyg på 4.6 stjärnor baserat på 7.5 recensioner. Har du en fråga om Gys Exagon 400 Flex CC/CV eller vill du ställa frågor till andra användare av produkten? Ställ en fråga
Sida 1/104
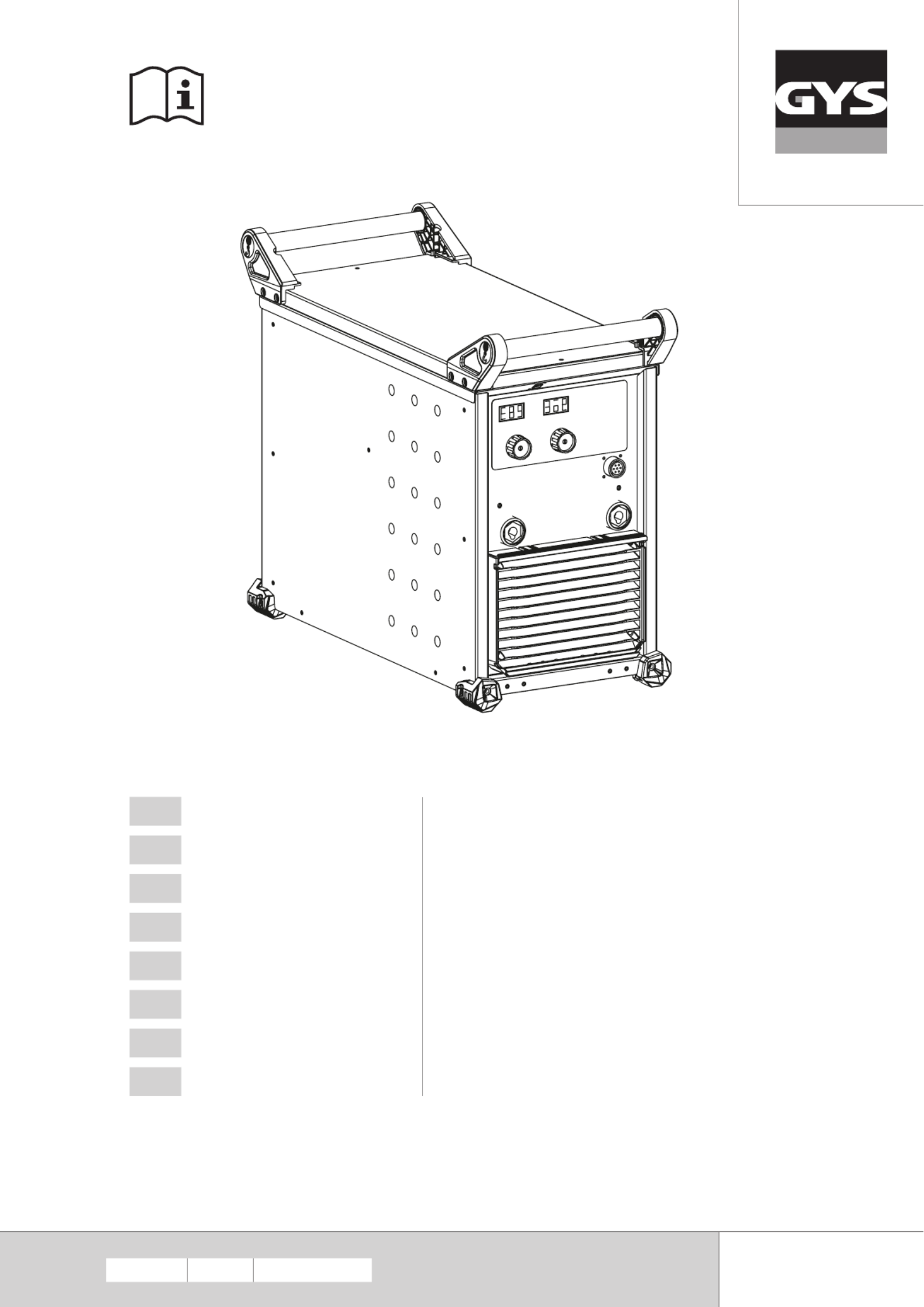
www.gys.fr
Find more languages of user manuals
FR 02 / 03-13 / 92-104 EXAGON 400 FLEX CC/CV
Générateur de soudage mulitvoltage
Multivoltage welding machine
EN 02 / 14-24 / 92-104
DE 02 / 25-35 / 92-104
ES 02 / 36-46 / 92-104
RU 02 / 47-58 / 92-104
NL 02 / 59-69 / 92-104
IT 02 / 70-80 / 92-104
PL 02 / 81-91 / 92-104
73502 V1 07/06/2023
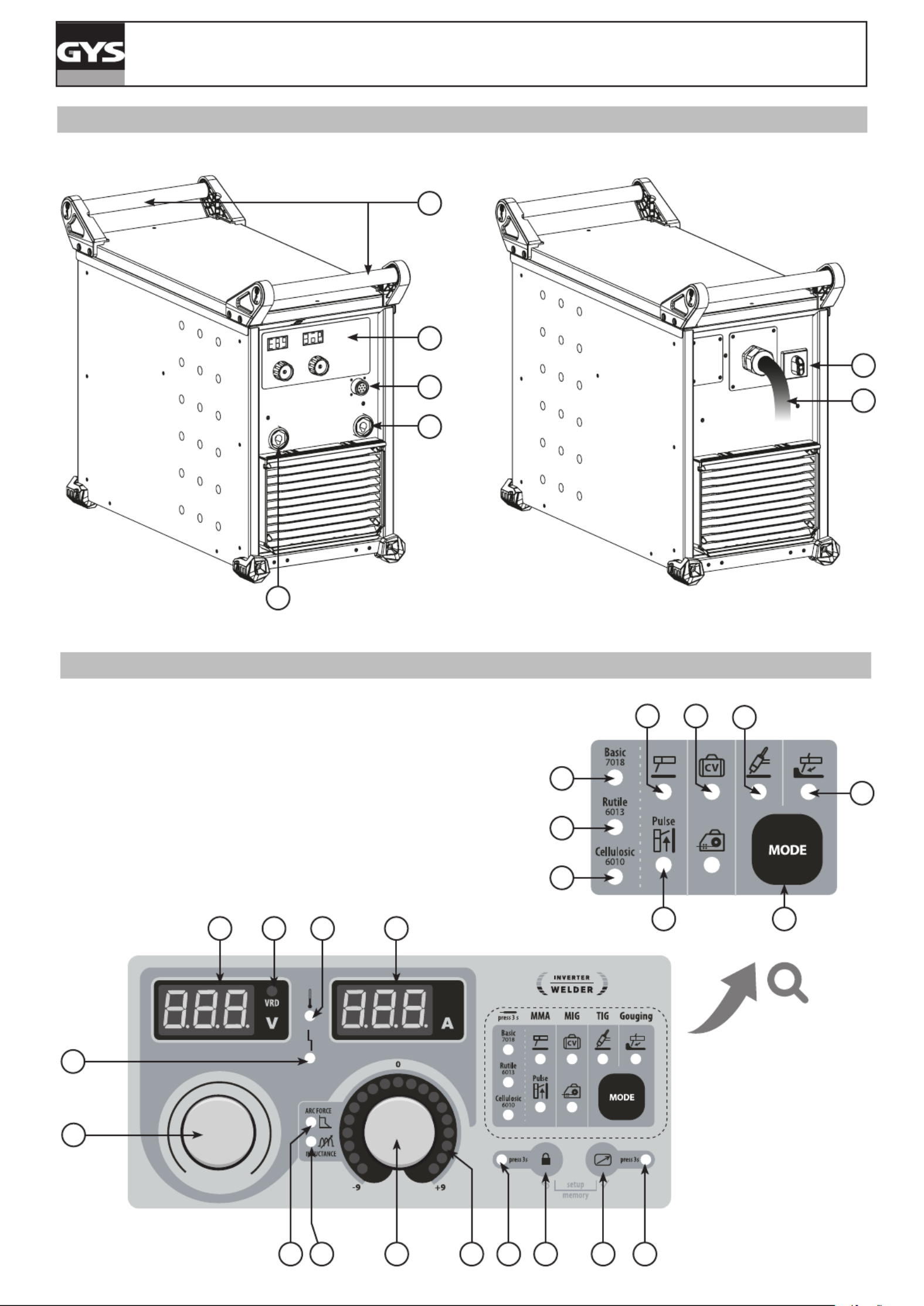
2
EXAGON 400 FLEX CC/CV
FIG-1
FIG-2
7
6
1
1 2 34
6
5
7 8 910 12 1311 14
15
16
17
19 23
22
21
2018
4
3
2
5
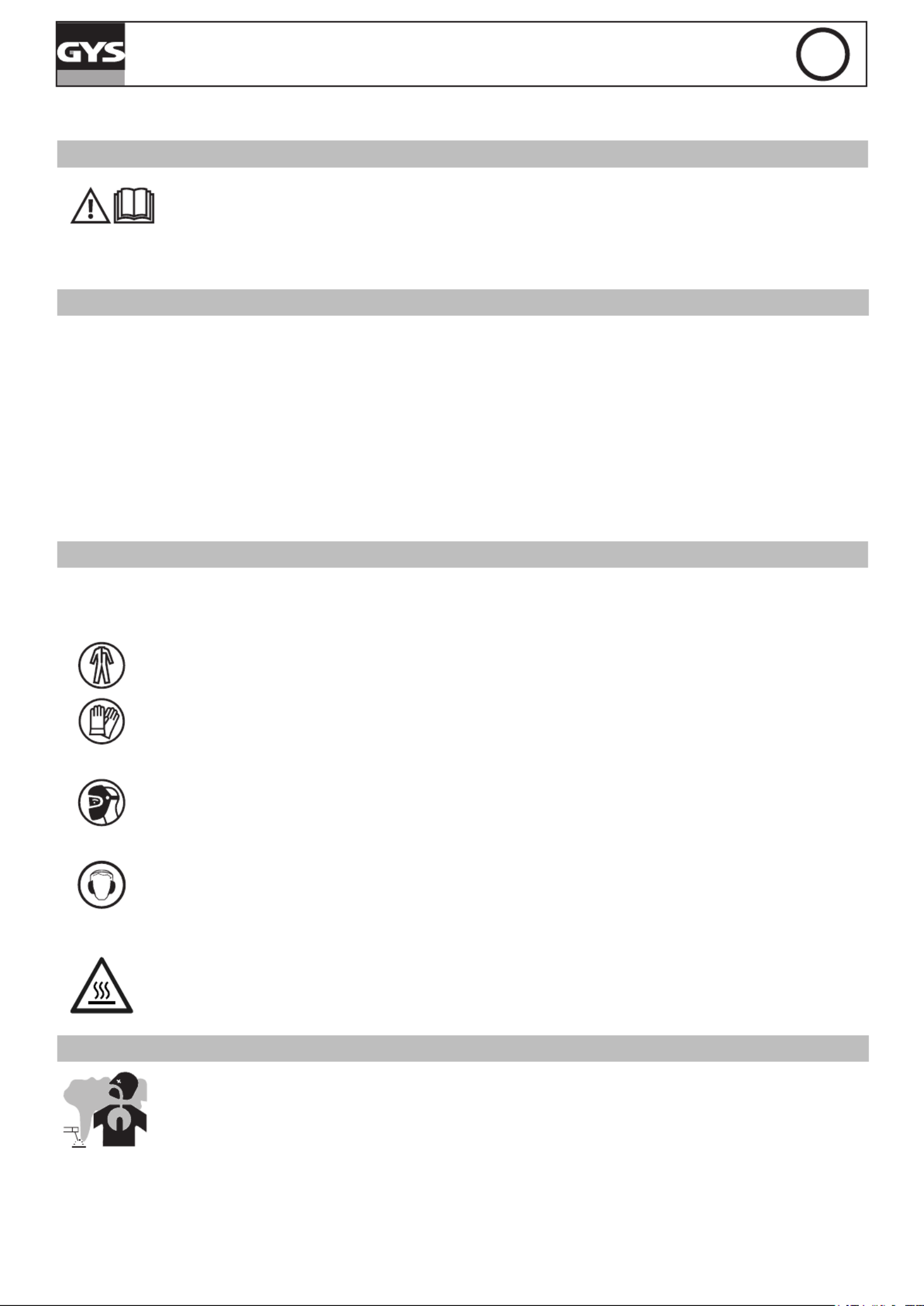
3
EXAGON 400 FLEX CC/CV FR
AVERTISSEMENTS - RÈGLES DE SÉCURITÉ
CONSIGNE GÉNÉRALE
Ces instructions doivent être lues et bien comprises avant toute opération.
Toute modication ou maintenance non indiquée dans le manuel ne doit pas être entreprise.
Tout dommage corporel ou matériel dû à une utilisation non-conforme aux instructions de ce manuel ne pourra être retenu à la charge du fabricant.
En cas de problème ou d’incertitude, consulter une personne qualiée pour manier correctement l’installation.
ENVIRONNEMENT
Ce matériel doit être utilisé uniquement pour faire des opérations de soudage dans les limites indiquées par la plaque signalétique et/ou le manuel.
Il faut respecter les directives relatives à la sécurité. En cas d’utilisation inadéquate ou dangereuse, le fabricant ne pourra être tenu responsable.
L’installation doit être utilisée dans un local sans poussière, ni acide, ni gaz inammable ou autres substances corrosives. Il en est de même pour son
stockage. S’assurer d’une circulation d’air lors de l’utilisation.
Plages de température :
Utilisation entre -10 et +40°C (+14 et +104°F).
Stockage entre -20 et +55°C (-4 et 131°F).
Humidité de l’air :
Inférieur ou égal à 50% à 40°C (104°F).
Inférieur ou égal à 90% à 20°C (68°F).
Altitude :
Jusqu’à 1000 m au-dessus du niveau de la mer (3280 pieds).
PROTECTIONS INDIVIDUELLES ET DES AUTRES
Le soudage à l’arc peut être dangereux et causer des blessures graves voire mortelles.
Le soudage expose les individus à une source dangereuse de chaleur, de rayonnement lumineux de l’arc, de champs électromagnétiques (attention
au porteur de pacemaker), de risque d’électrocution, de bruit et d’émanations gazeuses.
Pour bien se protéger et protéger les autres, respecter les instructions de sécurité suivantes :
An de se protéger de brûlures et rayonnements, porter des vêtements sans revers, isolants, secs, ignifugés et en bon état, qui
couvrent l’ensemble du corps.
Utiliser des gants qui garantissent l’isolation électrique et thermique.
Utiliser une protection de soudage et/ou une cagoule de soudage d’un niveau de protection susant (variable selon les applications).
Protéger les yeux lors des opérations de nettoyage. Les lentilles de contact sont particulièrement proscrites.
Il est parfois nécessaire de délimiter les zones par des rideaux ignifugés pour protéger la zone de soudage des rayons de l’arc, des
projections et des déchets incandescents.
Informer les personnes dans la zone de soudage de ne pas xer les rayons de l’arc ni les pièces en fusion et de porter les vêtements
adéquats pour se protéger.
Utiliser un casque contre le bruit si le procédé de soudage atteint un niveau de bruit supérieur à la limite autorisée (de même pour
toute personne étant dans la zone de soudage).
Tenir à distance des parties mobiles (ventilateur) les mains, cheveux, vêtements. Ne jamais enlever les protections carter du groupe
froid lorsque la source de courant de soudage est sous tension, le fabricant ne pourrait être tenu pour responsable en cas d’accident.
Les pièces qui viennent d’être soudées sont chaudes et peuvent provoquer des brûlures lors de leur manipulation. Lors d’intervention
d’entretien sur la torche ou le porte-électrode, il faut s’assurer qu’il/elle soit susamment froid(e) en attendant au moins 10 minutes
avant toute intervention. Le groupe froid doit être allumé lors de l’utilisation d’une torche refroidie eau an d’être sûr que le liquide
ne puisse pas causer de brûlures.
Il est important de sécuriser la zone de travail avant de la quitter an de protéger les personnes et les biens.
FUMÉES DE SOUDAGE ET GAZ
Les fumées, gaz et poussières émis par le soudage sont dangereux pour la santé. Il faut prévoir une ventilation susante,
un apport d’air est parfois nécessaire. Un masque à air frais peut être une solution en cas d’aération insusante. Vérier que
l’aspiration est ecace en la contrôlant par rapport aux normes de sécurité.
Attention le soudage dans les environnements réduits nécessite une surveillance à distance de sécurité. Par ailleurs le soudage de certains matériaux
contenant du plomb, cadmium, zinc ou mercure voire du béryllium peuvent être particulièrement nocifs.
Dégraisser également les pièces avant de les souder.
Les bouteilles doivent être entreposées dans des locaux ouverts ou bien aérés. Elles doivent être en position verticale et maintenues à un support ou
sur un chariot.
Le soudage doit être proscrit à proximité de graisse ou de peinture.
Produktspecifikationer
Varumärke: | Gys |
Kategori: | Inte kategoriserad |
Modell: | Exagon 400 Flex CC/CV |
Behöver du hjälp?
Om du behöver hjälp med Gys Exagon 400 Flex CC/CV ställ en fråga nedan och andra användare kommer att svara dig
Inte kategoriserad Gys Manualer
24 Februari 2025
10 Februari 2025
12 Oktober 2024
12 Oktober 2024
5 Oktober 2024
1 Oktober 2024
1 Oktober 2024
1 Oktober 2024
1 Oktober 2024
Inte kategoriserad Manualer
- Edelkrone
- Zendure
- Sogo
- RDL
- Videotel Digital
- Ewent
- Peavey
- Wilson
- ABE Arnhold
- Turbo Air
- Sonuus
- Ctek
- Studio Titan
- Aplic
- Blanco
Nyaste Inte kategoriserad Manualer
9 April 2025
9 April 2025
9 April 2025
9 April 2025
9 April 2025
9 April 2025
9 April 2025
9 April 2025
9 April 2025
9 April 2025