Microchip DSPIC33EP512GM604 Bruksanvisning
Microchip
Inte kategoriserad
DSPIC33EP512GM604
Läs gratis den bruksanvisning för Microchip DSPIC33EP512GM604 (130 sidor) i kategorin Inte kategoriserad. Guiden har ansetts hjälpsam av 10 personer och har ett genomsnittsbetyg på 5.0 stjärnor baserat på 5.5 recensioner. Har du en fråga om Microchip DSPIC33EP512GM604 eller vill du ställa frågor till andra användare av produkten? Ställ en fråga
Sida 1/130
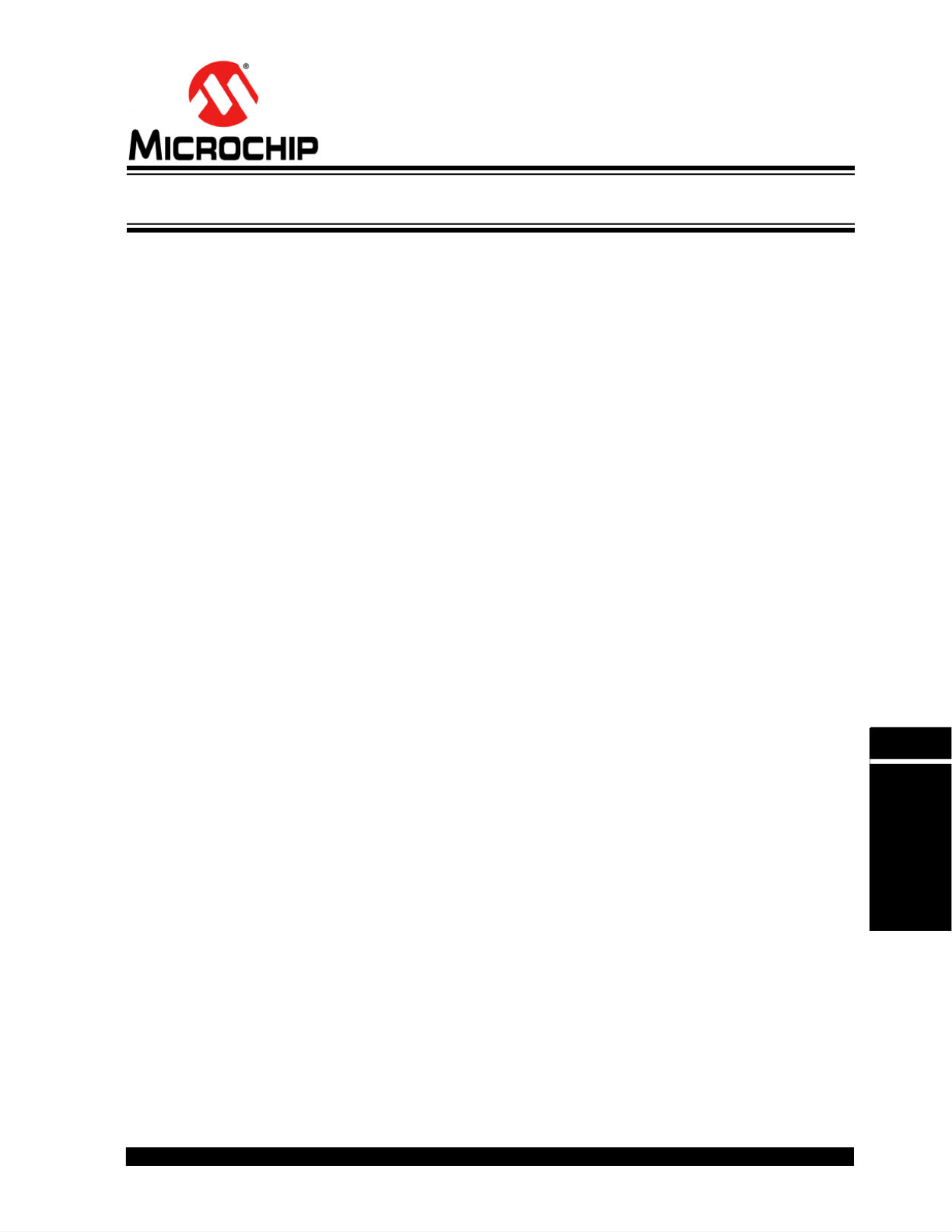
© 2010-2011 Microchip Technology Inc. DS70645C-page 14-1
High-Speed PWM
14
Section 14. High-Speed PWM
HIGHLIGHTS
This section of the manual contains the following major topics:
14.1 Introduction .................................................................................................................. 14-2
14.2 Features....................................................................................................................... 14-2
14.3 Control Registers ......................................................................................................... 14-3
14.4 Architecture Overview................................................................................................ 14-24
14.5 Module Description .................................................................................................... 14-27
14.6 PWM Operating Modes.............................................................................................. 14-33
14.7 PWM Generator......................................................................................................... 14-71
14.8 PWM Trigger.............................................................................................................. 14-87
14.9 PWM Interrupts.......................................................................................................... 14-98
14.10 PWM Fault Pins ......................................................................................................... 14-99
14.11 Special Features ...................................................................................................... 14-105
14.12 PWM Output Pin Control...........................................................................................14-111
14.13 Immediate Update of PWM Duty Cycle ................................................................... 14-113
14.14 Power-Saving Modes............................................................................................... 14-114
14.15 External Control of Individual Time Base(s)............................................................. 14-114
14.16 Application Information ............................................................................................ 14-115
14.17 Register Map............................................................................................................ 14-126
14.18 Related Application Notes........................................................................................ 14-127
14.19 Revision History ....................................................................................................... 14-128
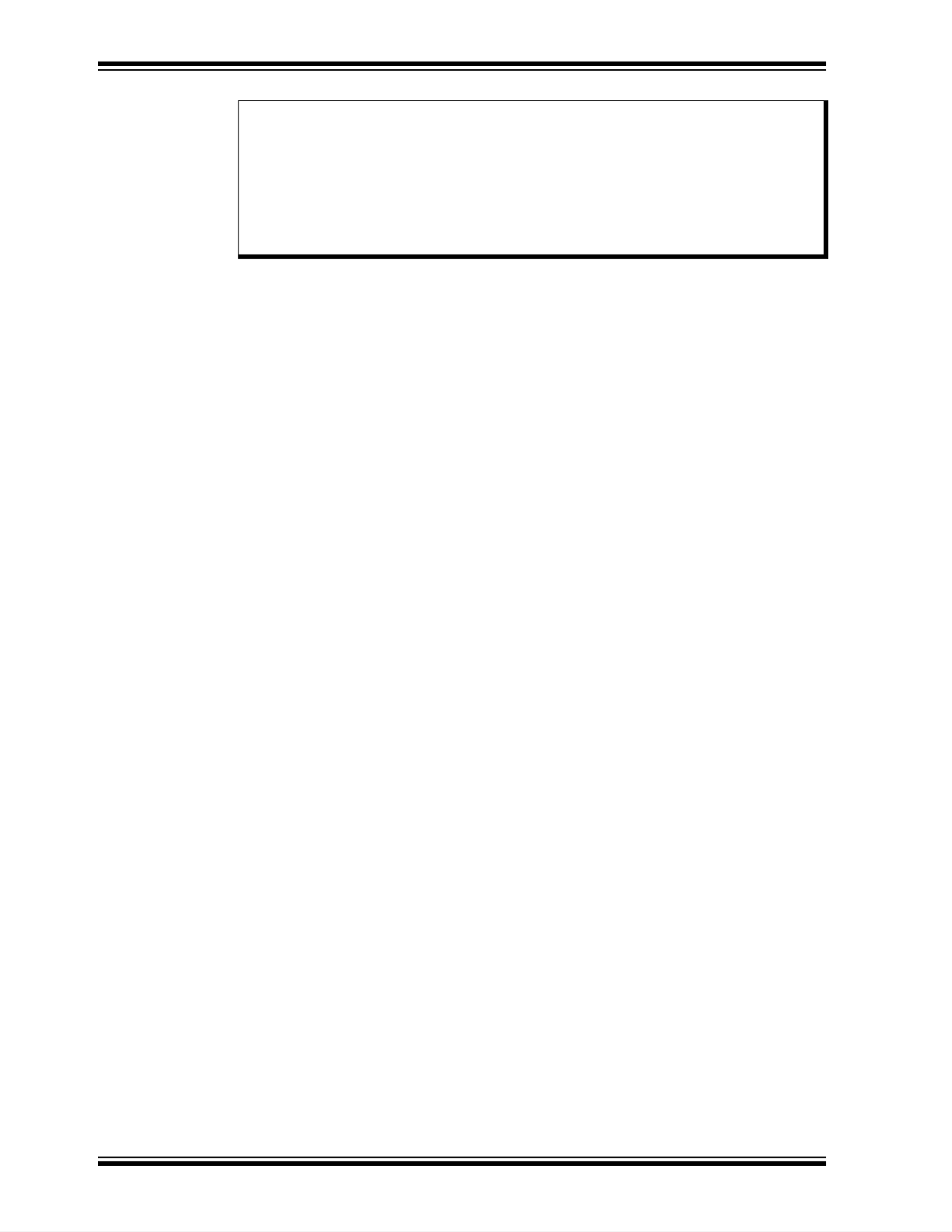
dsPIC33E/PIC24E Family Reference Manual
DS70645C-page 14-2 © 2010-2011 Microchip Technology Inc.
14.1 INTRODUCTION
This section describes the High-Speed Pulse-Width Modulator (PWM) module and its
associated operational modes. The High-Speed PWM module in the dsPIC33E/PIC24E
device family supports a wide variety of PWM modes and is ideal for power
conversion/motor control applications. Some of the common applications include:
• AC-to-DC converters
• DC-to-DC converters
• AC and DC motors: BLDC, PMSM, ACIM, SRM, etc.
• Inverters
• Battery chargers
• Digital lighting
• Uninterrupted Power Supply (UPS)
• Power Factor Correction (PFC) (e.g., Interleaved PFC and Bridgeless PFC)
14.2 FEATURES
The High-Speed PWM module consists of the following major features:
• Up to seven PWM generators, each with an individual time base
• Two PWM outputs per PWM generator
• Individual period and duty cycle for each PWM output
• Duty cycle, dead time, phase shift and frequency resolution equal to the system clock
source (TOSC)
• Independent fault and current-limit inputs for up to 14 PWM outputs
• Redundant Output mode
• Independent Output mode (this feature is not available on all devices)
• Push-Pull Output mode
• Complementary Output mode
• Center-Aligned PWM mode
• Output override control
• Special Event Trigger
• PWM capture feature
• Prescaler for input clock
• ADC triggering with PWM
• Independent PWM frequency, duty cycle and phase shift changes
• Leading-Edge Blanking (LEB) functionality
• Dead time compensation
• Output clock chopping
Note: This family reference manual section is meant to serve as a complement to device
data sheets. Depending on the device variant, this manual section may not apply to
all dsPIC33E/PIC24E devices.
Please consult the note at the beginning of the “High-Speed PWM” chapter in the
current device data sheet to check whether this document supports the device you
are using.
Device data sheets and family reference manual sections are available for
download from the Microchip Worldwide Web site at: http://www.microchip.com
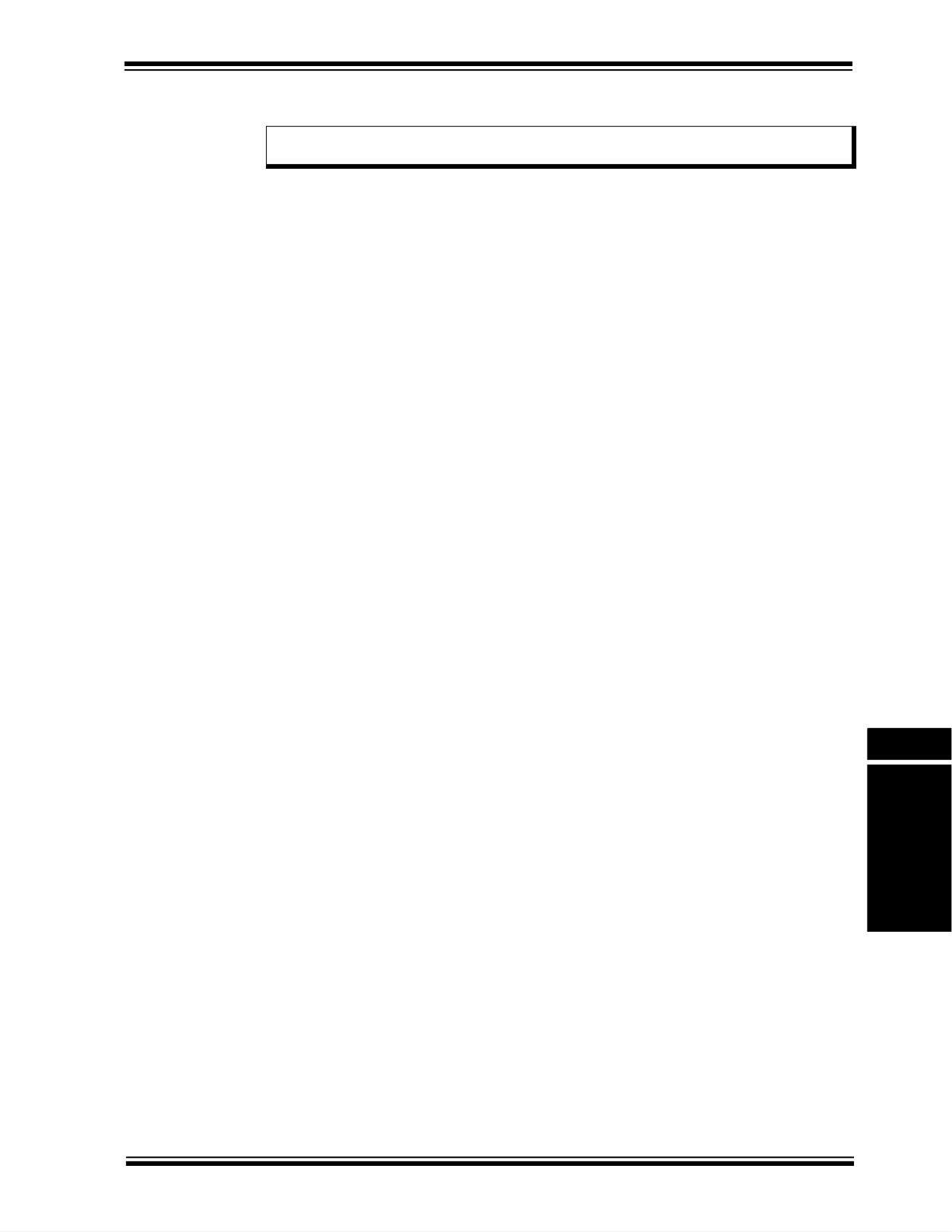
© 2010-2011 Microchip Technology Inc. DS70645C-page 14-3
Section 14. High-Speed PWM
High-Speed PWM
14
14.3 CONTROL REGISTERS
The following registers control the operation of the High-Speed PWM module:
•PTCON: PWM Time Base Control Register
- Enables or disables the High-Speed PWM module
- Sets the Special Event Trigger for the ADC
- Enables or disables immediate period updates
- Selects the synchronizing source for the master time base
- Specifies synchronization settings
•PTCON2: PWM Clock Divider Select Register 2
Provides the clock prescaler to the PWM master time base
•PTPER: Primary Master Time Base Period Register
Provides the PWM time period value
•STCON: PWM Secondary Master Time Base Control Registe (1)
- Enables or disables immediate period updates based on the secondary master time base
- Selects the synchronization source for the secondary master time base
- Specifies the synchronization setting for secondary master time base control
• STCON2: PWM Secondary Clock Divider Select Register 2(1)
Provides the clock prescaler to the PWM secondary master time base
•STPER: Secondary Master Time Base Period Register(1)
Provides the secondary master time base period value
•MDC: PWM Master Duty Cycle Register
Provides the PWM master duty cycle value
•SEVTCMP: PWM Special Event Compare Register
Provides the compare value that is used to trigger the ADC module
•SSEVTCMP: PWM Secondary Special Event Compare Register(1)
Provides the compare value that is used to trigger the ADC module based on the
secondary master time base
•CHOP: PWM Chop Clock Generator Register
- Provides the chop clock frequency
- Enables or disables the chop clock generator
•PWMKEY: PWM Unlock Register(1)
Writes the unlock sequence to allow writes to the IOCONx and FCLCONx registers
•PWMCONx: PWM Control Register
- Enables or disables fault interrupt, current-limit interrupt and primary trigger interrupt
- Provides the interrupt status for fault interrupt, current-limit interrupt and primary trigger
interrupt
- Selects the type of time base (master time base or independent time base)
- Selects the type of duty cycle (master duty cycle or independent duty cycle)
- Controls Dead Time mode
- Enables or disables Center-Aligned mode
- Controls the external PWM Reset operation
- Enables or disables immediate updates of the duty cycle, phase offset, independent time
base period
•IOCONx: PWM I/O Control Register
- Enables or disables PWM pin control feature (PWM control or GPIO)
- Controls fault/current limit override values
- Enables PWMxH and PWMxL pin swapping
- Controls the PWMxH and PWMxL output polarity
- Controls the PWMxH and PWMxL output if any of the following modes is selected:
• Complementary mode
• Push-Pull mode
• True Independent mode
Note: Not all registers are available on all devices. Refer to the “High-Speed PWM”
chapter in the specific device data sheet for availability.
Produktspecifikationer
Varumärke: | Microchip |
Kategori: | Inte kategoriserad |
Modell: | DSPIC33EP512GM604 |
Behöver du hjälp?
Om du behöver hjälp med Microchip DSPIC33EP512GM604 ställ en fråga nedan och andra användare kommer att svara dig
Inte kategoriserad Microchip Manualer
12 Mars 2025
12 Mars 2025
6 Mars 2025
5 Mars 2025
4 Mars 2025
4 Mars 2025
2 Mars 2025
2 Mars 2025
2 Mars 2025
2 Mars 2025
Inte kategoriserad Manualer
- Polsen
- Lastolite
- Paidi
- PATLITE
- Rock N Roller
- Redrock Micro
- Solid
- Ideal
- OXI Instruments
- Teka
- Davita
- Petsafe
- Geze
- Byron
- Peerless
Nyaste Inte kategoriserad Manualer
9 April 2025
9 April 2025
9 April 2025
9 April 2025
9 April 2025
9 April 2025
9 April 2025
9 April 2025
9 April 2025
9 April 2025